Flexible Epoxy Resin Flow for Fuel Resistant Tank Repair in Gas ApplicationsFlexible Epoxy Resin Flow to
Repair Fuel Resistant Tanks in Gas Applications
In the realm of gas storage and transportation, the integrity of fuel - resistant tanks is of paramount
importance.The integrity of fuel-resistant tanks is paramount in the world of gas storage and transport. Any
compromise in the tank's structure can lead to hazardous situations, including gas leaks, which pose
significant risks to safety and the environment.Gas leaks and other hazardous situations can be caused by a
compromise in the tank structure. This poses a significant risk to safety and to the environment. One
innovative solution that has emerged to address tank repair needs is the use of flexible epoxy resin
flow.Flexible epoxy resin flow is a new innovative solution to tank repair.
Fuel - resistant tanks used in gas applications are exposed to a variety of harsh conditions.Fuel-resistant
tanks used for gas applications are subjected to a wide range of harsh conditions. They must withstand the
corrosive nature of gases, temperature fluctuations, and mechanical stresses.They must be able to withstand
the corrosive properties of gases, temperature fluctuations and mechanical stresses. Over time, these
factors can cause cracks, holes, or other forms of damage to the tank walls.These factors can damage the
tank walls over time by causing cracks, holes or other types of damage. Traditional repair methods often
have limitations, such as lack of flexibility, poor adhesion, or insufficient resistance to the fuel and gas
environment.Traditional repair methods have limitations such as poor adhesion or lack of flexibility.
Flexible epoxy resin offers several key advantages for fuel - resistant tank repair.Flexible epoxy resin has
several advantages for the repair of fuel-resistant tanks. First and foremost, its flexibility allows it to
adapt to the movement and expansion/contraction of the tank due to temperature changes. Gas tanks can
experience significant thermal cycling, especially in outdoor storage or during transportation in different
climates.Gas tanks are subject to thermal cycling, particularly when stored outdoors or transported in
different climates. A rigid repair material may crack or separate from the tank surface under these
conditions, but a flexible epoxy resin can maintain its integrity and bond with the tank.Under these
conditions, a rigid repair material can crack or separate from a tank's surface. However, if the tank is
coated with a flexible epoxy resin, the epoxy resin will maintain its integrity and remain bonded to the
tank.
The flow - ability of the flexible epoxy resin is another crucial feature.Another important feature is the
flow-ability of the flexible epoxy. When applied, it can easily penetrate into small cracks and
irregularities in the tank surface.It can easily penetrate small cracks or irregularities on the tank
surface. This ensures a thorough and comprehensive repair, filling in even the tiniest voids.This ensures
that even the smallest voids are filled, resulting in a thorough repair. In gas tank repair, this is
essential as even a minuscule leak can be extremely dangerous.This is crucial in gas tank repairs, as even
the smallest leak can be dangerous. The resin's ability to flow into these areas helps to create a seamless
and continuous repair layer that effectively seals the damaged region.The resin's ability flow into these
areas creates a seamless and continual repair layer that effectively seals damaged regions.
Resistance to gas and fuel is a non - negotiable requirement for any repair material used in these tanks.Any
material used to repair these tanks must be resistant to fuel and gas. Flexible epoxy resins are formulated
to be highly resistant to the chemical components of gases and fuels.Flexible epoxy resins have been
formulated to be highly resistance to the chemical components in fuels and gases. They can withstand the
solvents, hydrocarbons, and other substances present in the gas environment without deteriorating or losing
their physical properties.They can withstand solvents, hydrocarbons and other substances in the gas
environment, without deteriorating their physical properties. This chemical resistance ensures that the
repaired tank can continue to function safely and effectively over an extended period.This chemical
resistance ensures the repaired tank will continue to function effectively and safely for a long period of
time.
The process of using flexible epoxy resin for fuel - resistant tank repair typically begins with a thorough
inspection of the tank.The process of using flexible Epoxy resin for fuel-resistant tank repair usually
begins with a thorough examination of the tank. This involves identifying the location and extent of the
damage.This involves determining the extent and location of the damage. Once the damage is assessed, the
tank surface is prepared.After assessing the damage, the tank's surface is prepared. This may include
cleaning the area to remove any dirt, grease, or corrosion products.Cleaning the area is necessary to remove
any dirt or corrosion products. Abrasion may also be carried out to roughen the surface, which improves the
adhesion of the epoxy resin.Abrasion can also be used to roughen the surface and improve the adhesion.
After surface preparation, the flexible epoxy resin is mixed according to the manufacturer's
instructions.After surface preparation, the flexible Epoxy resin is mixed according the instructions of the
manufacturer. The mixed resin is then carefully applied to the damaged area.The resin mixture is then
applied carefully to the damaged area. Depending on the size and nature of the damage, it can be applied
using a brush, roller, or in some cases, a spray gun.Depending on its size and nature, it can be applied
with a roller, brush, or spray gun. As the resin flows over the damaged surface, it begins to bond with the
tank material.As the resin flows across the damaged surface it bonds with the tank material. It is important
to ensure an even application to avoid creating thin or thick spots that could potentially lead to weak
points in the repair.It is important to apply the resin evenly to avoid creating thin or dense spots that
could lead to weak areas in the repair.
Once the epoxy resin is applied, it needs to cure.The epoxy resin must cure after it is applied. The curing
process may take a few hours to several days, depending on the type of resin and environmental
conditions.The curing process can take anywhere from a few hours up to several days depending on the type
resin and the environmental conditions. During this time, the resin hardens and forms a strong, durable bond
with the tank.During this period, the resin hardens, forming a strong and durable bond with your tank. It is
crucial to follow the recommended curing conditions, such as temperature and humidity, to ensure optimal
performance of the repaired area.To ensure the best performance of the repaired area, it is important to
adhere to the recommended curing conditions.
In addition to its use in repairing existing damage, flexible epoxy resin can also be used as a preventive
measure.Flexible epoxy resin is not only useful for repairing damage but can also be used to prevent future
damage. Applying a layer of the resin to the inner or outer surface of a new or relatively undamaged tank
can provide an additional layer of protection against corrosion and mechanical damage.The resin can be
applied to the inner or exterior surface of a tank that is relatively new or undamaged. This will provide an
extra layer of protection from corrosion and mechanical damage. This proactive approach can extend the
lifespan of the tank and reduce the likelihood of future repairs.This proactive approach will extend the
life of the tank, and reduce the need for future repairs.
In conclusion, flexible epoxy resin flow is a game - changing solution for fuel - resistant tank repair in
gas applications.Flexible
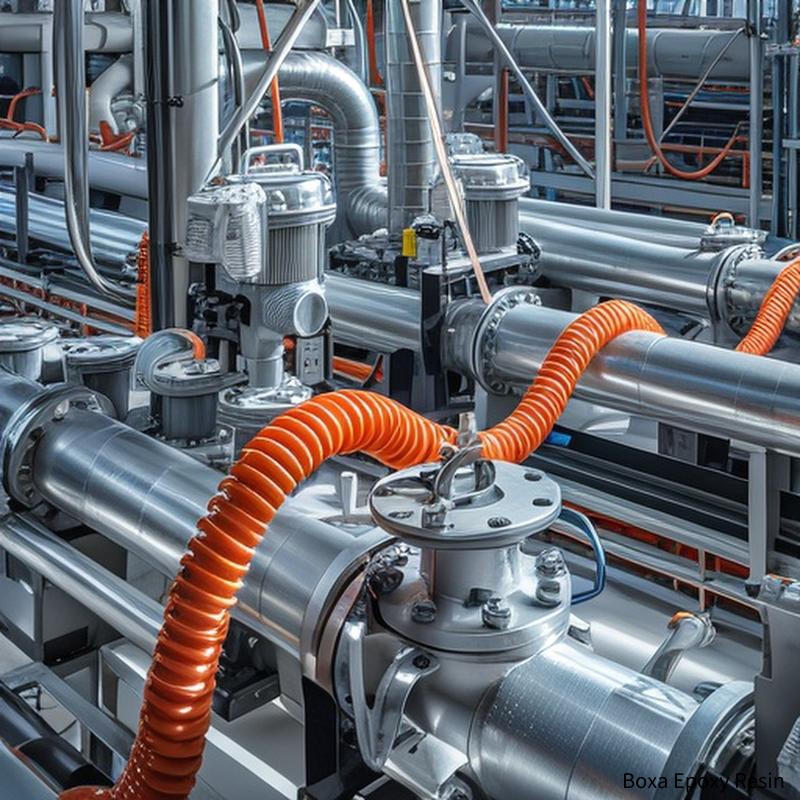
epoxy resin
flow can be a game-changing solution for fuel-resistant tank repair in gas applications. Its flexibility,
flow - ability, and fuel resistance make it an ideal choice for ensuring the safety and integrity of gas
storage and transportation tanks.Its flexibility, fuel resistance, and flow-ability make it a great choice
for ensuring safety and integrity in gas storage and transport tanks. By following proper application and
curing procedures, this innovative material can effectively repair damaged tanks and prevent future issues,
safeguarding both people and the environment from the potential hazards associated with gas leaks.This
innovative material can be used to repair damaged tanks, and prevent future problems, by following the
correct application and curing procedure. It protects both people and the environmental from the potential
hazards of gas leaks. As the demand for safe and reliable gas storage and transportation continues to grow,
the importance of such advanced repair technologies cannot be overstated.The importance of advanced repair
technologies is not to be underestimated as the demand for safe, reliable gas storage and transport
continues to increase.