hardest epoxy resin hardman heat resistant for metal lem low viscosity
The Hardest Epoxy Resin Hardman: Heat - Resistant for Metal with Low ViscosityThe Hardest Epoxy Hardman: Heat-Resistant for Metals with Low Viscosity
In the world of materials, epoxy resins have carved out a significant niche due to their versatility and unique properties.Epoxy resins have created a niche in the world of materials due to their versatility. They also possess unique properties. Among them, the search for the hardest epoxy resin, especially one that is heat - resistant for metal applications and has a low viscosity, is of great importance in various industries.The search for the hardest epoxy resin is important in many industries, especially for those that are heat-resistant for metal applications and have a low viscosity.
Epoxy resins are thermosetting polymers that, when cured, form a cross - linked structure.When cured, epoxy resins form a cross-linked structure. This cross - linking is what gives them their remarkable strength and durability.This cross-linking is what gives them remarkable strength and durability. The "hardest" epoxy resin in this context refers to one that can withstand high levels of stress, abrasion, and mechanical impact.In this context, the "hardest" epoxy is one that can withstand abrasion and mechanical impact, as well as high levels of stress. Such a resin is essential for protecting metal surfaces, which are often subjected to harsh conditions in industrial settings.This resin is vital for protecting metal surfaces that are often exposed to harsh conditions.
Heat resistance is another crucial aspect.Heat resistance is also a crucial factor. Metals are used in numerous applications where they are exposed to elevated temperatures.Metals are used for many applications that are exposed to high temperatures. For example, in the automotive industry, engines generate a substantial amount of heat.In the automotive industry for example, engines generate considerable heat. Epoxy resins applied to metal engine components need to maintain their integrity and adhesion even at high temperatures.Epoxy resins used on metal engine components must maintain their integrity and adhesion at high temperatures. A heat - resistant epoxy resin for metal can prevent corrosion, thermal degradation, and mechanical failure.A heat-resistant epoxy resin for metals can prevent corrosion, thermal degrading, and mechanical failure. It acts as a thermal barrier, protecting the metal from the detrimental effects of heat.It acts as a heat barrier, protecting metal from the damaging effects of heat.
The low viscosity of the epoxy resin is equally significant.Low viscosity is also important. Low - viscosity epoxy resins are easier to handle and process.Low-viscosity epoxy is easier to process and handle. They can flow more freely, allowing for better penetration into pores and irregularities on the metal surface.They flow more easily, allowing better penetration into the pores and irregularities of the metal surface. This ensures a more complete and uniform coating.This results in a more uniform and complete coating. In manufacturing processes, low - viscosity resins can be quickly and efficiently applied, reducing production time and costs.Low - viscosity epoxy resins can be applied quickly and efficiently in manufacturing processes, reducing costs and production time. For instance, in the electronics industry, where metal components need to be precisely coated, a low - viscosity epoxy resin can be dispensed accurately, covering small and intricate parts without forming air bubbles or uneven layers.In the electronics industry for example, where metal components must be coated precisely, a low-viscosity epoxy can be dispensed with accuracy, covering small and complex parts without creating air bubbles or uneven layering.
The development of the hardest epoxy resin with heat resistance for metal and low viscosity involves careful selection of raw materials.The development of the hardest epoxy resin with low viscosity and heat resistance for metals requires careful selection of raw material. Epoxy monomers, curing agents, and additives all play a crucial role.All three components, epoxy monomers, curing agent, and additives, play a vital role. Epoxy monomers with high - molecular - weight and rigid structures contribute to the hardness of the cured resin.Epoxy monomers that have a high - molecular weight and rigid structure contribute to the hardness. Curing agents are chosen based on their ability to promote cross - linking at appropriate temperatures and rates.Curing agents must be chosen for their ability to promote cross-linking at the right temperatures and rates. Additives such as fillers can enhance heat resistance and hardness.Fillers and additives can increase heat resistance and hardness. For example, ceramic fillers can significantly improve the heat - dissipation properties of the epoxy resin, making it more suitable for high - temperature applications.Ceramic fillers, for example, can improve the heat dissipation of epoxy resins, making them more suitable for high-temperature applications.
In the aerospace industry, this type of epoxy resin is used to bond metal components.This type of epoxy resin can be used in the aerospace industry to bond metal components. The high - strength and heat - resistant properties ensure the structural integrity of the aircraft, especially in areas like the engine and exhaust systems.The high-strength and heat-resistant properties of this epoxy resin ensure structural integrity, especially for areas such as the engine and exhaust system. The low viscosity allows for easy application during the manufacturing process, ensuring a seamless bond between different metal parts.Low viscosity makes it easy to apply during the manufacturing process. This ensures a seamless bonding between metal parts.
Testing and quality control are essential in the production of such epoxy resins.In order to produce epoxy resins, it is essential to test and control quality. Hardness is typically measured using methods like the Shore hardness test.Shore hardness tests are commonly used to measure the hardness of epoxy resins. Heat resistance is evaluated through techniques such as thermogravimetric analysis (TGA), which determines the weight loss of the resin as a function of temperature.Heat resistance can be evaluated using techniques like thermogravimetric analyses (TGA), that determine the weight loss in the resin as temperature changes. Viscosity can be measured using viscometers, ensuring that the resin meets the required low - viscosity specifications.Viscosity is measured with viscometers to ensure that the resin meets low-viscosity specifications.
In conclusion, the hardest epoxy resin that is heat - resistant for metal and has a low viscosity is a valuable material in modern manufacturing.The hardest epoxy resin, which is heat-resistant for metals and has a lower viscosity, is a valuable product in modern manufacturing. Its properties make it suitable for a wide range of applications, from protecting metal structures in industrial plants to enabling the production of high - performance electronics and aerospace components.Its properties make this resin suitable for a variety of applications. These range from protecting metal structures within industrial plants to enabling high-performance electronics and aerospace components. As technology continues to advance, further research and development in this area are likely to lead to even more improved epoxy resin formulations, meeting the ever - growing demands of various industries.Further research and development will likely lead to improved
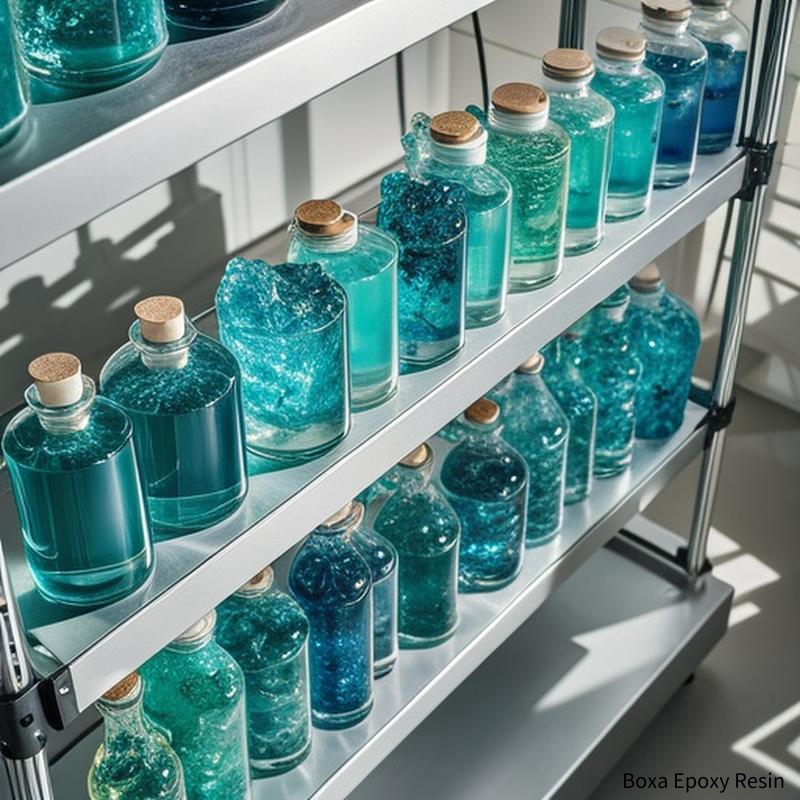
epoxy resin formulations as technology advances.