Title: Working with 60% Plastic to Epoxy Resin and Hardener Stone Coat 5 MinuteTitle: Working with 60% plastic to Epoxy Resin & Hardener Stone Coat in 5 Minutes
In the world of DIY projects, crafting, and even some industrial applications, the combination of different materials can lead to some truly remarkable results.Combining different materials in DIY projects, crafts, and even industrial applications can produce some amazing results. One such interesting blend is the use of 60% plastic along with epoxy resin and the Hardener Stone Coat 5 Minute product.A blend of 60% plastic, epoxy resin, and Hardener Stone Coat 5-Minute product is one such interesting mix. This unique mixture opens up a realm of possibilities, from creating durable and aesthetically pleasing art pieces to solving various repair and construction - related challenges.This unique blend opens up a world of possibilities. From creating durable and aesthetically pleasing artwork to solving repair and construction-related challenges, this mixture is a game changer.
Plastic, being a versatile and widely available material, forms the bulk of this combination at 60%.Plastic, a versatile material that is widely available, makes up 60% of this combination. Plastics come in different types, each with its own set of properties.Plastics are available in many different types, with each having its own properties. For this particular application, the choice of plastic can greatly influence the final outcome.The choice of plastic is important for this application. If we consider using a type of plastic that is lightweight and has some flexibility, it can add a certain resilience to the end - product.Consider using a lightweight plastic with some flexibility to add resilience to the final product. For example, polyethylene or polypropylene plastics, which are commonly found in packaging materials, can be shredded or melted down and incorporated into the epoxy - hardener mixture.Polyethylene or polypropylene, which are common in packaging materials, can either be shredded down or melted and incorporated into an epoxy-hardener mixture.
The epoxy resin, on the other hand, is a crucial component.The epoxy resin is the key component. Epoxy resins are known for their excellent adhesive properties, high strength, and chemical resistance.Epoxy resins have excellent adhesive properties and are chemically resistant. When mixed with the appropriate hardener, in this case, the Hardener Stone Coat 5 Minute, a chemical reaction occurs.A chemical reaction occurs when the Hardener Stone Coat 5-Minute is mixed with the appropriate epoxy resin. This reaction causes the resin to cure, transforming from a liquid state into a solid, hardened mass.This chemical reaction causes the resin, which was in a liquid form, to become a solid mass. The Hardener Stone Coat 5 Minute lives up to its name by providing a relatively quick - curing process.The Hardener 5 Minute Stone Coat lives up to its name, providing a relatively fast - curing procedure. In just five minutes, the mixture starts to set, which is highly beneficial for projects where time is of the essence.The mixture begins to set in just five minutes. This is great for projects that are time-sensitive.
When we add 60% plastic to this epoxy - hardener system, several things happen.When we add 60 % plastic to the epoxy-hardener system, a few things happen. Firstly, the plastic can act as a filler.The plastic can be used as a filler. By incorporating plastic particles, we can reduce the amount of pure epoxy resin needed, which can be cost - effective, especially for large - scale projects.We can reduce the amount needed of epoxy resin by incorporating plastic particles. This can be cost-effective, especially for large-scale projects. The plastic particles distribute within the resin matrix, and as the epoxy cures, they become an integral part of the final structure.Plastic particles are distributed within the resin matrix and, as the epoxy cures they become an integral component of the final structure. This can enhance the mechanical properties of the cured product.This can improve the mechanical properties of a cured product. For instance, the plastic can improve the impact resistance.The plastic can, for example, improve impact resistance. If the end - product is likely to be subjected to knocks or drops, the plastic - reinforced epoxy is better equipped to withstand such forces without cracking or breaking.The plastic-reinforced epoxy is better able to withstand knocks and drops without cracking or breaking.
Secondly, from an aesthetic perspective, the plastic can add unique visual elements.Second, from an aesthetic point of view, the plastic can create unique visual elements. Depending on the color and texture of the plastic used, it can create interesting patterns or a marbled effect within the epoxy.The color and texture can create interesting patterns, or even a marbling effect in the epoxy. Clear plastics can be used to create a semi - transparent, almost frosted look, while colored plastics can be mixed to achieve a vibrant and multi - hued finish.Clear plastics are ideal for creating a semi-transparent, almost frosted finish, while colored plastics mixed together can create a vibrant, multi-hued finish. This makes it ideal for creating decorative items such as countertops, tabletops, or even art sculptures.This makes it perfect for decorative items like countertops, tabletops or even art sculptures.
Let's consider a practical example of using this 60% plastic - epoxy - hardener combination.Let's look at a practical application of this 60% plastic-epoxy-hardener combination. Suppose we want to create a custom - made, durable floor covering for a small workshop.Imagine we need to create a durable, custom-made floor covering for a small shop. We start by collecting an appropriate amount of plastic waste, perhaps from discarded plastic pipes or plastic crates.We begin by collecting a suitable amount of plastic waste. This could be from discarded plastic pipes, or plastic crates. We then shred this plastic into small, manageable pieces.We then shred the plastic into manageable pieces. Next, we measure out the epoxy resin and the Hardener Stone Coat 5 Minute according to the manufacturer's instructions.Then, we follow the manufacturer's instructions to measure out the Hardener Stone Coat 5-Minute and epoxy resin. The 60% plastic is then gradually added to the mixed epoxy - hardener solution while stirring continuously.The 60 % plastic is added gradually to the epoxy-hardener solution, while stirring continuously.
As we pour the mixture onto the prepared floor surface, we can use a spreader or a trowel to ensure an even distribution.Spreader or trowel can be used to ensure an even application of the mixture as we pour it onto the floor surface. Within minutes, as the Hardener Stone Coat 5 Minute starts to work its magic, the mixture begins to set.As the Hardener 5 Minute Stone Coat begins to work, the mixture will begin to set within minutes. The plastic particles are locked in place, creating a solid and robust floor covering.The plastic particles are firmly anchored in place to create a robust and solid floor covering. This floor not only has the strength and durability of epoxy but also the added benefits of the plastic reinforcement, such as better abrasion resistance.This floor has the strength and durability that epoxy provides, but also benefits from the plastic reinforcement such as improved abrasion resistance.
However, working with this combination also comes with its challenges.But working with this combination is not without its challenges. One of the main issues is ensuring proper mixing.The main issue is mixing properly. The plastic particles need to be evenly distributed throughout the epoxy - hardener mixture.The plastic particles must be evenly distributed in the epoxy-hardener mixture. If not, there can be areas with an excess of plastic or areas where the epoxy resin is not properly reinforced.The epoxy resin may not be reinforced properly or there could be areas with excess plastic. This can lead to uneven curing and potentially weaker spots in the final product.This can lead uneven curing, and possibly weaker spots in your final product. To overcome this, thorough and continuous mixing is essential.It is important to mix continuously and thoroughly. Using a mechanical mixer, if possible, can help achieve a more homogeneous blend.If possible, using a mechanical blender can help you achieve a more homogeneous mixture.
Another consideration is the compatibility of the plastic with the epoxy resin.Compatibility of the plastic and epoxy resin is another consideration. Some plastics may not bond well with the epoxy, resulting in a poor - quality end - product.Some plastics will not bond well to the epoxy resin, resulting in an end-product of poor quality. It may be necessary to perform some small - scale tests beforehand to determine which plastics work best with the chosen epoxy - hardener system.Some small-scale tests may be required to determine which plastics are compatible with the chosen epoxy-hardener system. Additionally, the curing process of the epoxy - hardener can be affected by environmental factors such as temperature and humidity.The curing process for the epoxy-hardener is also affected by environmental factors, such as temperature and moisture. In colder or more humid conditions, the 5 - minute curing time of the Hardener Stone Coat may be extended, and extra care needs to be taken to ensure proper curing.In colder and more humid conditions, it may be necessary to extend the 5-minute curing time for the Hardener Stone Coat.
In conclusion, the use of 60% plastic in combination with
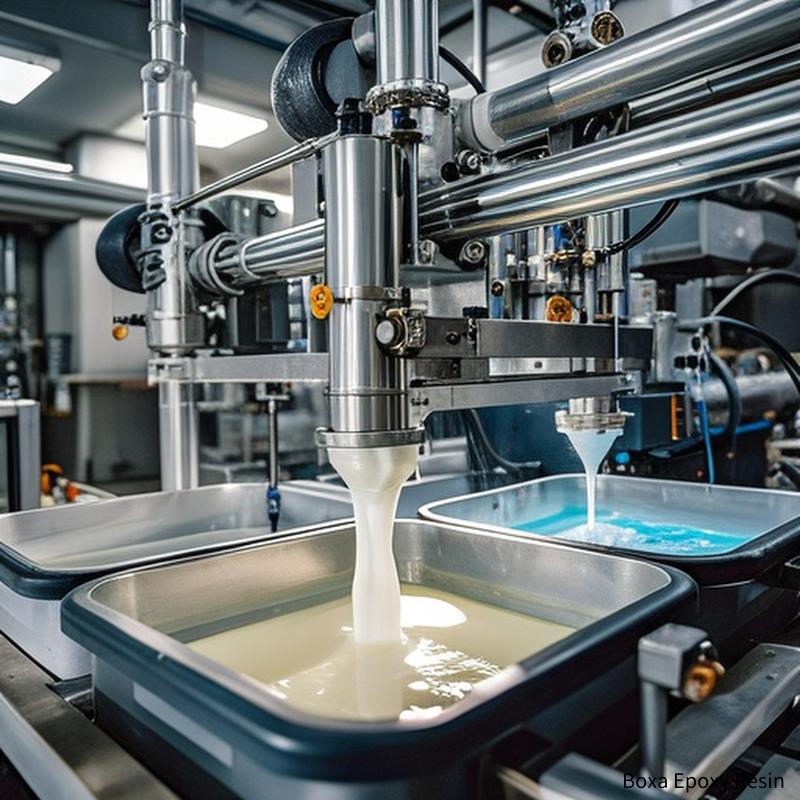
epoxy resin and the Hardener Stone Coat 5 Minute offers a world of opportunities for DIY enthusiasts, artisans, and even small - scale industries.The use of 60% of plastic in combination with epoxy and the Hardener 5 Minute Stone Coat offers a wide range of possibilities for DIY enthusiasts, small-scale industries, and even artisans. It allows for the creation of unique, durable, and cost - effective products.It allows the creation of unique and durable products that are cost-effective. By understanding the properties of each component, addressing the challenges associated with their combination, and being creative in their application, one can unlock the full potential of this fascinating material blend.Understanding the properties of the components, addressing the challenges of their combination, and using creativity in their application can help unlock the full potential for this fascinating material mix. Whether it's for functional items or decorative masterpieces, this 60% plastic - epoxy - hardener combination is a tool in the hands of those looking to innovate and create.This 60% plastic - epoxy-hardener combination can be used to create functional items or decorative masterpieces.